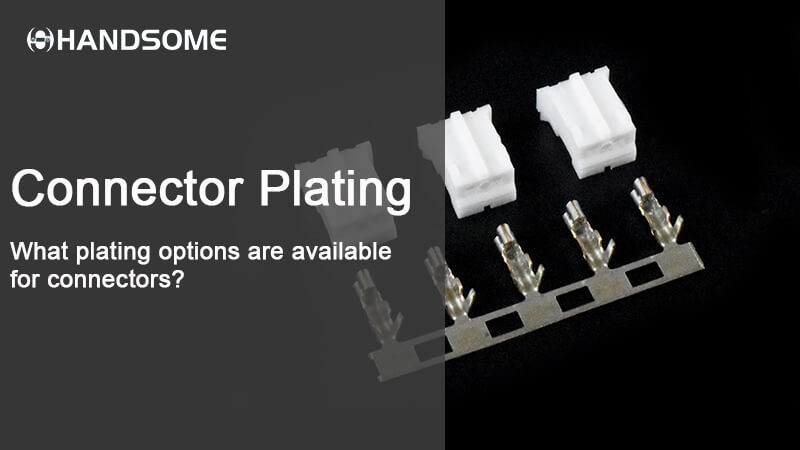
Table of Contents
For connector products to achieve stable electrical connection and transmission performance, high-quality metal terminals (contacts) are crucial, such as pins, blade spring, etc., all belong to the category of terminal components.
Currently, most of the metal materials used in terminals in the connector industry are copper. However, although copper terminals are cheap, they also have the disadvantage of being easily oxidized and corroded, which causes the contact resistance of the connector to increase during use, thus affecting the current conduction efficiency of the connector product.
Moreover, compared to precious metals such as gold and silver, copper’s electrical conductivity is slightly inferior. In high-frequency or high-speed transmission application scene, the conductivity of copper terminals may have some negative effects on signal transmission performance.
So, how to improve the contact performance and usability of metal terminals while ensuring manufacturing economy?
Connector manufacturers have wisely worked hard on surface treatment processes, using electroplating processes such as gold plating, silver plating,
And tin plating to meet the application needs of connector products in different application environments and achieve the purpose of enhancing the stability and reliability of connector products. .
“Electroplating” itself is not difficult to understand. In short, cleaning steps such as decontamination, degreasing and degreasing are first carried out on the metal terminals of the connector product,
And then the electroplating solution is plated on the surface of the terminal (using the principle of electrolysis to plate a thin layer of other metals or alloy on the surface of the metal terminal), making it have better electrical conductivity, corrosion resistance, and plug-and-pull resistance.
The electroplating process of the connector plays an important role in improving the performance and reliability of the connector. This process can enhance the conductivity of the metal terminal contact surface, reduce resistance and signal loss during the connector contact process, and improve the quality of signal transmission, and stability, extend the plug-in use life of the connector, and even improve the appearance of the connector.
Like most electronic components, the quality of countless sub-components and processes directly affects the quality and performance of the finished product.
For PCB-grade connectors, these factors include pin material, plastic type, quality of the molded plastic body, coplanarity of the tails, quality of surface treatment (plating), selecting the correct connector plating, manufacturing/assembly process and packaging, etc. wait.
Plating affects the life and quality of a terminal or socket; it affects corrosion resistance, conductivity, solderability and cost.
There are many options for plating terminals, generally divided into four categories: noble metals, inert metals, alloys and dispersions.
The first three categories are already established and used, while dispersion is just beginning to emerge to address the need for high-power connectivity in electric vehicle charging and similar applications.
We begin with a brief review of basic electroplating system concepts, then describe the properties of noble metals, inert metals, and alloys, and conclude with a brief overview of the potential advantages of dispersions.
Plating systems are typically multi-layer structures, where the top layer can be a relatively thin coating. Inert metal surfaces like tin are often found in consumer products.
Industrial, military, medical and other high-performance applications often turn to noble metals.
Noble metals are often used as alloys. For example, pure gold is too soft for many applications, while gold alloyed with cobalt, nickel, or iron, known as “hard gold,” is used to provide greater durability.
Other precious metals such as silver can also be used as alloys to increase hardness.
Noble Metals
gold plated
Gold is highly conductive even at low voltages. It has excellent oxidation and corrosion resistance compared to other options. It is ideal for use in environments with high humidity or frequent heat cycles.
Gold is typically specified for high reliability, low voltage or low current applications. Gold is used in high mating cycles because it is strong and has good wear properties.
Our gold is made from a cobalt alloy, which increases its hardness. We also recommend gold for use in harsh environments.
Gold is a noble metal, which means it is not very responsive to the environment.
Additionally, sometimes gold is necessity because as connectors become miniaturized, the contacts are too small to generate much normal force.
Therefore, low normal force directs the demand for gold plating.
The disadvantages of gold are mainly cost, then porosity of the thinner plating, and some nuances regarding solderability. Specifically, many customers have “successfully” soldered these products, but they did not solder to gold because the gold would dissolve in the molten solder.
They are soldered to nickel underneath the gold. So, technically speaking, it is correct to say that gold has poor solderability.
Silver Plated
Silver performs well in high power applications. It is less expensive than gold and is a good choice for larger, high current contacts.
Palladium Plated
Palladium has high electrical and thermal conductivity and is resistant to corrosion. It is harder than gold or silver, making it a good choice for applications that require more durability.
Rhodium plated
Rhodium is harder than palladium and is resistant to corrosion and acids. It is ideal for applications requiring good wear resistance and high hardness.
Inert Metal
Tin Plated
Tin is non-toxic and therefore suitable for some medical applications. Tin is a lower cost alternative to gold and offers excellent solderability. Unlike gold, tin is not a noble metal. Tin plating begins to oxidize when exposed to air. Therefore, tinned contact systems require larger normal forces and longer contact wipe areas to break through this oxide film.
Tin is usually preferred because it is relatively low cost and suitable for applications with a small number of mating cycles with appropriate normal force.
Nickel Plated
Nickel is very hard, durable and corrosion-resistant. Its combination of durability and high conductivity make it suitable for high-use applications.
Copper is one of the most conductive metals, but it requires a protective layer to prevent corrosion. It is often used as a basis for subsequent metal plating.
Metal Alloy
White bronze is a non-magnetic alloy composed of copper, tin and zinc that is more conductive than nickel. It is ideal for many medical and RF connectors.
Palladium-nickel alloy is corrosion-resistant and has low contact resistance. It has good solderability and can handle a large number of mating cycles. Palladium-nickel plating often flashes gold.
Electroless nickel plating can be applied to both conductive and non-conductive surfaces. Electroless nickel plating layers contain up to 14% phosphorus.
The higher the phosphorus content, the greater the corrosion resistance, but the hardness decreases.
Nickel-phosphorus alloy has high wear resistance and corrosion resistance. They have good weldability but have lower electrical conductivity than other alloys.
Silver Graphite Dispersion
Silver-graphite dispersions have been developed for use in contacts in high-power applications such as electric vehicle chargers. It combines the properties of fine silver and hard silver.
The fine silver matrix provides high conductivity and the graphite increases wear resistance and supports high cycle life.
Uniform and random dispersion of graphite particles is one of the keys to high durability
X-ray spectroscopic scan of the contact surface shows the even distribution of graphite on the surface
How to choose?
Selective gold and tin plating is the most popular plating option because it offers designers the best of both worlds.
The contact area, the critical area for interface between contacts and terminal pins and signal transmission, has the reliability of gold.
Tail soldered to the circuit board with lower cost and improved tin solderability.
FAQ
Can gold be soldered?
This is a complex issue. Some people say you shouldn’t solder gold-plated components to a PCB.
Others say yes, but with caution! You should be cautious as the gold plating will dissolve in the solder, there is a risk of solder contamination, and there is a risk of gold embrittlement.
Regarding the embrittlement issue, once the gold contribution to the weight of the solder joint reaches 3% or 5%, embrittlement becomes a problem.
Regarding the dissolution of gold in solder, as explained above, the solder paste is not soldered to the gold plate.
The gold plate dissolves in the molten solder and the soldering occurs on the nickel base plate
Can I mate gold-plated and tin-plated connectors? What will happen to electrochemical corrosion?
When selecting a connector for your application, it is important to select a mating connector with similar plating material in the contact area.
Dissimilar metals in contact areas can cause galvanic corrosion. Galvanic corrosion usually occurs on metals with different electronegativities.
The diagram shows how different plating materials react with each other in terms of electrical potential.
According to this diagram, gold and tin have high electrical potentials.
Summarize
A wide range of plating options are available to support varying levels of conductivity, environmental ruggedness, durability and other application needs.
With the development of graphite dispersion plating materials, the traditional choice between precious metals, inert metals and various alloys is expanding.