The Ultimate Guide To Servo Motor Cable: The Knowledge You Need To Know
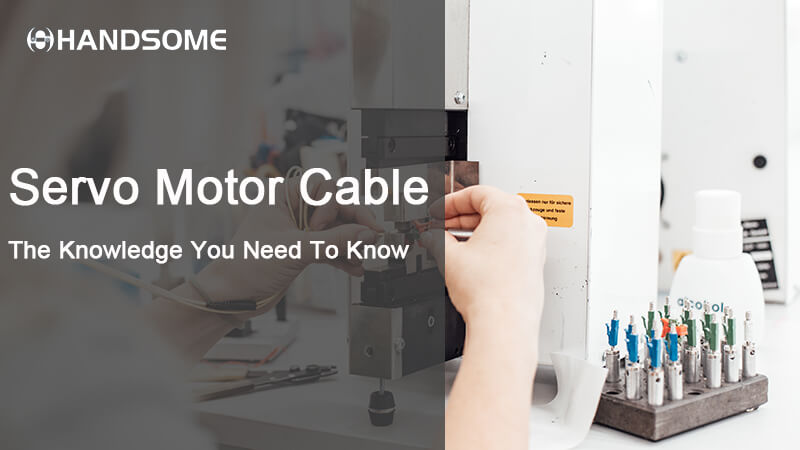
Table of Contents
Introduction of Servo Motor Cables
Servo Motor Cable with high flexibility, abrasion resistance, tensile strength, corrosion resistance, bending resistance, tensile strength, twisting resistance, anti-interference ability, anti-aging and a series of unique characteristics, so that as a connection with servo motor special cables of servo automatic control system and servo motors can be a perfect combination of the operation of the use of servo motors, and greatly enhance the servo motors (control motors, Implement the motor) of the work efficiency. Direct point is that the servo motor cable is the connection cable, but this is for servo motor special, not easy to break, shielding the external signal interference.
What is Servo Motor Cables?
Servo Motor Cable (Servo Harness or Servo Cable) refers to the electrical connection harness used to connect between a servo motor and a servo drive. It is the bridge between the mechanical and electrical systems and is responsible for transmitting critical signals such as power, communication signals, and encoder feedback.
Servo motor is a high-precision drive that can accurately control its position and speed based on control signals. Servo motor wiring harnesses usually consist of power, signal, encoder, and motor wires, and use specific connection methods and standardized wire color matching to ensure proper connection and communication.
As servo motors require very high precision, servo motor wiring harnesses must also be of high quality and reliability, which can avoid problems of short-circuiting wires and electrical interference, thus ensuring the normal operation of servo motors. At the same time, the servo motor wiring harness also needs to be designed and manufactured according to the specific servo motor model and specifications to ensure that it matches the servo motor perfectly.
Basics of Servo Motors
Understanding Servo Motor Systems
What is Servo System?
Servo system, also known as a randomizer system, is a feedback control system used to precisely follow or reproduce a process. Servo system makes the object’s position, orientation, state and other output controlled quantities can follow the input target (or given value) of the arbitrary change of the automatic control system.
Its main task is to control the command requirements, power amplification, transformation and regulation and other processing, so that the drive output torque, speed and position control is very flexible and convenient. Servo system consists of three parts: controller, power driver and motor.
The main function of the servo drive is to control the servo motor, its role is similar to the role of the frequency converter in the ordinary AC motor, belongs to a part of the servo system, mainly used in high-precision positioning system.
Generally through the position, speed and torque of three ways to control the servo motor, to achieve high precision positioning of the drive system, is the transmission technology of the high-end products, so the servo motor can be understood as absolute obedience to the control signal command of the motor.
What is Servo Motor?
The word “servo” comes from the Latin word “servus”, which means a servant who follows his master’s instructions and works faithfully and quickly.
Servo Motor is an indirect variable speed device that converts electrical signals, it is a part of servo system.
Servo motor is a high-precision, high-speed electric device that accomplish a specified rotational motion under the command of a control system. Its main structure consists of two parts, the stator, which is made of laminated silicon steel sheets, and the rotor, which is a permanent magnet.
Servo motors are able to respond very quickly, have a high power density and a wide range of operating frequencies. To be used in a variety of high-precision, high-speed positioning and motion control. The working principle is to use pulse signals to provide precise control of the rotation angle and rotation speed of the servo motor.
The Types of Servo Motor
ACIM:Asynchronous Induction Motor
IM:Induction Motor
ASM:Asynchronous Servo Motor
AFE:Active Front End
VFD:Variable Frequency Drive
Comparison of servo motor advantages and disadvantages | |||
Types | SM Type AC Servo Motor | IM Type AC Servo Motor | DC Servo Motor |
Advantages |
|
|
|
Disadvantage |
|
|
|
Image | ![]() | ![]() | ![]() |
What is Servo Driver?
Servo drives, also known as “servo controllers” and “servo amplifiers”, are controllers used to control servo motors. , a part of the servo system, mainly used in high-precision positioning system. Generally through the position, speed and torque of three ways to control the servo motor, to achieve high-precision positioning of the drive system, is currently the high-end products of drive technology.
At present, the mainstream servo drive are used digital signal processor (DSP) as the control core, can realize the more complex control algorithms, digital, networked and intelligent. Power devices are generally used to intelligent power module (IPM) as the core design of the drive circuit, IPM internal integration of the drive circuit, at the same time with over-voltage, over-current, overheating, under-voltage and other fault detection and protection circuits, in the main circuit is also added to the soft-start circuit, in order to minimize the start-up process of the impact of the drive.
Servo drive is an important part of modern motion control, is widely used in industrial robots and CNC machining centers and other automation equipment. In particular, servo drives applied to control AC permanent magnet synchronous motors have become a research hotspot at home and abroad. The current design of AC servo drives generally use vector control based on the current, speed, position 3 closed-loop control algorithm. The algorithm in the speed closed-loop design is reasonable or not, for the entire servo control system, especially the speed control performance plays a key role.
Role of Cables in Servo Motor Functionality
Cables play a vital role in the functionality of servo motors by facilitating the communication between the servo drive/controller and the motor. Servo motors are highly precise devices used in various applications such as robotics, manufacturing, and automation. Here are a few key factor where cables play a role in servo motor functionality:
Power Supply:
Servo Motor Power Cables are responsible for supplying power to the servo motor. Servo Motor Power cables transmit the electrical energy needed between drives and motors and enable it to perform specified tasks.
Feedback Signals:
Servo motors is feedback devices with encoders or resolvers that provide position, speed, and torque feedback to the controller. Feedback signals are transmitted via specialized cables, allowing the controller to continually adjust the operation of the motor to achieve the desired performance.
Communication:
Communication cables connect the servo motor to the servo drive or controller. These cables transmit control signals from the controller to the motor, directing its motion and regulating its performance. Communication may involve a variety of protocols, such as pulse width modulation (PWM) or other digital communication protocols.
Data Transmission:
High-quality cables are essential for reliable data transmission between the controller and the servo motor. Data integrity is critical for accurate feedback and precise control of motor motion.
Shielding:
Servo motor cables are often shielded to protect the signal from electromagnetic interference (EMI) or radio frequency interference (RFI). This shielding helps maintain signal integrity and ensures proper servo system operation, especially in industrial environments with a variety of electrical equipment.
Flexibility:
Cables used in servo systems must be flexible to accommodate drag chain motion of the motor. The flexibility of the cable ensures smooth movement without compromising signal quality or risking damage to the cable.
Durability:
Servo motors are often required to be used in harsh industrial environments, so cables must be durable and able to withstand mechanical stress, abrasion and other harsh conditions. This ensures the long-term reliability of the servo system.
In short, cables are an integral part of a servo motor system, transmitting power, control signals and feedback data between the motor and the controller. Selecting high-quality, well-designed cables is critical to the reliable and accurate operation of servo motors in a variety of applications.
Types of Servo Motor Cable
Currently, because servo cable are used to connect the components in a servo system and provide electrical control, so there are huge market needs in industrial equipment market.
The voltage of servo encoder is relatively low, and it needs to come with a shield to resist electromagnetic interference in order to protect the signal from interference. Servo motor cable harness is mainly divided into servo power cable, servo encoder cable and servo brake cable these 3 types.
Why said servo harness consists of servo power cable, encoder cable, and brake cable?
That 3 types Servo harnesses are only the most basic configuration, can make the servo drive and motor with the normal operation, if you need to add other configurations, then you need to match the corresponding network cables and other corresponding equipment cables.
Servo Motor Power Cable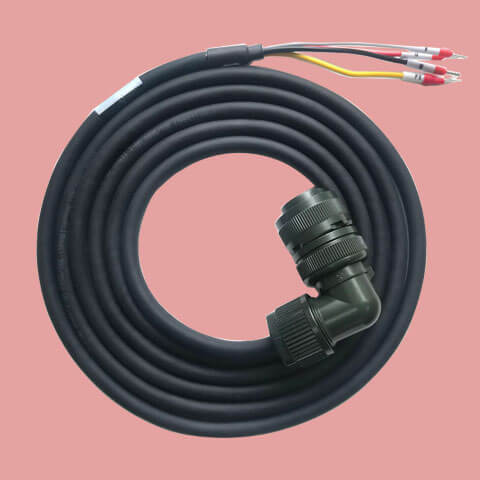
The servo power cable is the cable that transmits electrical energy, and its function is to drive the motor to run, and at the same time monitor the motor torque change.
The servo power cable consists of two parts, one is the connection cable between the servo driver and the power supply, and the other part is the connection cable between the servo driver and the servo motor.
Servo power cable uses high-strength, bend-resistant shield tinned copper wire , which effectively prevents signal loss and electromagnetic interference, and has excellent transmission performance.
Servo Motor Encoder Cable
Servo encoder cable, also known as servo signal cable, is used in servo systems as a signal cable harness for encoding signal transmission and feedback.
Servo Motor Brake Cable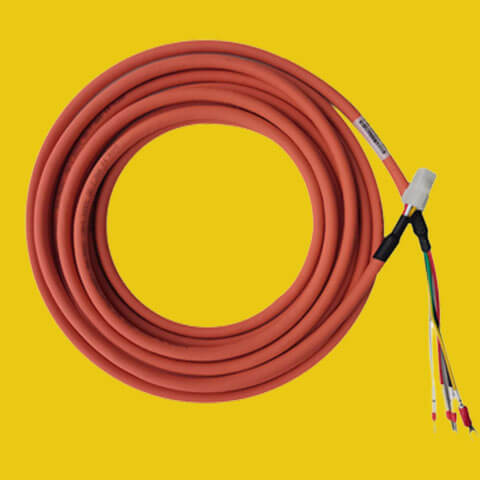
Servo brake cable is used to make drive emergency stop, in the drive to the motor power supply in an emergency, servo drive brake cable will automatically cut off the power, play a protective role.
The Main Brand of Servo Motor Cable
Chinese Brand
雷赛Leadshine Servo Motor Cable
禾川 HCFA Servo Motor Cable
英威腾 INVT Servo Motor Cable
信捷 XINJE Servo Motor Cable
艾薇图 EVTA Servo Motor Cable
汇川 Inovance Servo Motor Cable
三协3X Motion Servo Motor Cable
东元 TECO Servo Motor Cable
儒竞RUKING Servo Motor Cable
埃斯顿 ESTUN Servo Motor Cable
韦德 WEIDE Servo Motor Cable
艾威图EVTR Servo Motor Cable
德力西DELIXI Servo Motor Cable
英威腾INVT Servo Motor Cable
迈信Maxsine Servo Motor Cable
睿能Raynen Servo Motor Cable
Japanese Brand
松下 Panasonic Servo Motor Cable
发那科 Fanuc Servo Motor Cable
三菱 Mitsubishi Servo Motor Cable
三洋 Sanya Servo Motor Cable
European Brand
西门子 Siemens Servo Motor Cable
施而耐德 Schneider Servo Motor Cable
Key Features to Consider
High Flexible and bend radius of servo motor cables are important considerations to ensure proper operation between cables and connected equipment. Servo motor cables are used to transmit control signals and power to servo motors, which are commonly used in robotics, automation and other precision applications.
Flexible:
High Flexible: Servo motor cables often need to move and bend in different directions, especially in dynamic applications. The high Flexible allows the cable to withstand repeated bending without damage.
Stranded conductors: Stranded conductor cables are often more flexible than solid conductor cables. Stranded conductors make cables easier to bend.
Bend radius:
MINIMUM BENDING RADIUS: The manufacturer specifies a minimum bending radius for servo motor cables, indicating the smallest radius at which the cable can be bent without causing damage. Exceeding the minimum bend radius can result in damage of the insulation and conductors, affecting the performance of the cable.
Cable Construction: The construction of the cable, including the materials used for insulation and shielding, affects the flexibility and bend radius of the cable. Some cables are specially designed to improve flexibility.
Cable type and design:
Shielded: Shielded cables protect signals from external interference. While shielding adds some stiffness, it is critical to maintaining signal integrity in electrically noisy environments.
Sheath Material: The sheath material affects the cable’s abrasion resistance, chemicals and the environment. For example, TPE (thermoplastic elastomer) jacket is known for its flexibility and durability.
Application Considerations:
Stationary vs. Continuous Motion: The nature of the application (stationary or continuous motion) will affect the requirements of the cable. Cables used for continuous motion may require greater flexibility and resistance to repeated bending.
Installation guidelines:
Follow manufacturer’s recommendations: Always follow the manufacturer’s cable installation guidelines and specifications, including bend radius limitations.
Support and strain relief: Proper cable support and strain relief mechanisms help prevent excessive bending and reduce the risk of damage.
It is important to consult the servo motor and cable manufacturer’s documentation for specific recommendations and guidelines. Using cables that meet the requirements of the application ensures reliable performance and minimizes the risk of premature failure.
What is servo motor cable used for?
Servo motor system has some performance advantages in the accuracy, moment frequency, overload, AC servo motor can be used in the situation where the control accuracy of position, speed and torque is very high, such as in CNC machine tools, electronic manufacturing equipment, packaging machinery, textile machinery, robotics, plastics machinery, medical machinery, food machinery, and other fields have been widely used; at the same time, the promotion of intelligent manufacturing makes servo motor in the emerging industry application scale growth rapidly, the overall market scale growth space is larger.
The following are some common servo harness applications:
Industrial automation:
servo harnesses are widely used in industrial machinery and robotic systems. By connecting servo motors and drives, servo harnesses enable motion control systems to accurately control position, speed and acceleration, thereby improving productivity and product quality.
CNC machine:
In CNC machine, servo harnesses are used to connect servo motors and CNC systems to achieve high-precision control of tool position and workpiece movement. This application ensures that the machine achieves precise trajectories in operations such as cutting, milling and drilling.
Robotics:
Servo harnesses play a key role in robotics. They connect the robot’s joints and actuators and enable the robot to perform complex movements and tasks. The use of servo harnesses enables robots to achieve high-speed, high-precision and coordinated movements for use in manufacturing, logistics, medical and service robotics.
Medical Equipment:
In the medical field, servo harnesses are widely used in medical equipment such as CT scanners, X-ray machines, and surgical robots. These devices require precise motion control and positional positioning, and servo harnesses provide reliable signal transmission and power supply to ensure high performance and safety.
Aerospace:
In aerospace, servo harnesses are used to connect components such as rudders, motorized valves and actuators in aircraft.
How to Choose Right Servo Motor Cables for Your Application?
Choosing the right servo motor cables for your application is a critical step in ensuring reliable and efficient operation. Here’s a step-by-step guide to help you make an informed decision:
Understand Your Application:
Define the specific requirements of your application, including the type of machinery, movement dynamics, and environmental conditions.
Voltage and Current Ratings:
Check the servo motor specifications for voltage and current requirements. Choose cables that can safely handle the power demands of your servo system.
Cable Type:
Consider the type of signals your servo motor requires (e.g., power, feedback signals). Select cables designed for these specific purposes, such as power cables and feedback cables.
Flexibility and Bend Radius:
Determine the level of cable flexibility needed based on your application’s motion characteristics. For dynamic applications with frequent movement, choose high-flex cables. Adhere to the minimum bend radius specifications to prevent damage.
Environmental Conditions:
Evaluate the environmental factors, including temperature, humidity, and exposure to chemicals or oils. Choose cables with appropriate ratings for your application environment.
Mechanical Stress and Abrasion:
Assess the potential for mechanical stress and abrasion in your application. Select cables with robust outer jackets and additional features like armor or braiding for enhanced protection.
Shielding:
Consider the electromagnetic environment of your application. If there is a risk of electromagnetic interference (EMI), choose cables with effective shielding to maintain signal integrity.
Cable Length:
Determine the length of the cable run and assess voltage drop considerations. Ensure that the selected cable can maintain voltage levels over the required distance.
Compliance and Certification:
Verify that the chosen cables comply with relevant industry standards and regulations. Look for certifications that validate the cables for specific applications or industries.
Installation Considerations:
Plan the cable routing to minimize stress and bending during operation. Use proper support structures and strain relief mechanisms to prevent damage.
Cost Considerations:
Balance technical requirements with budget constraints. While it’s essential to meet the specifications of your application, consider cost-effective options that still provide the necessary performance and reliability.
Consult with Experts:
Reach out to cable manufacturers, distributors, or industry experts for guidance. They can provide valuable insights based on their expertise and experience.
Review Manufacturer Recommendations:
Always refer to the servo motor manufacturer’s recommendations and guidelines for cable selection. They often provide specific requirements to ensure optimal performance.
By carefully considering these factors and consulting relevant documentation, you can choose servo motor cables that meet the unique needs of your application, promoting efficiency and longevity in your system.
Advancements in Servo Motor Cable Technology
High-Flex Materials:
Advances in materials science have led to the development of high-flex materials for cable jackets. These materials enhance the flexibility and durability of servo motor cables, allowing them to withstand continuous motion and frequent bending.
Hybrid Cables:
Some advancements involve the integration of multiple functions into a single cable. Hybrid cables may combine power conductors with signal or feedback conductors, reducing the number of cables needed for a particular application.
Signal Integrity and EMI Protection:
Ongoing efforts focus on improving signal integrity and protection against electromagnetic interference (EMI). Enhanced shielding and insulation technologies help maintain the quality of control signals, especially in electrically noisy environments.
Temperature Resistance:
Servo motor cables are often subjected to a wide range of temperatures in various applications. Advances in cable materials aim to improve temperature resistance, ensuring reliable performance in both high and low-temperature environments.
Oil and Chemical Resistance:
Applications in industrial settings may expose cables to oils and chemicals. Cable manufacturers have been working on developing cables with improved resistance to these substances to prolong cable life in challenging environments.
Smart Cables and Connectivity:
With the rise of Industry 4.0 and the Internet of Things (IoT), there is a trend toward smart cables that incorporate sensors or other monitoring capabilities. These cables may provide real-time data on cable health, temperature, and other relevant parameters.
Reduced Downtime Solutions:
Cable designs that prioritize easy installation, maintenance, and replacement contribute to reducing downtime. Quick-connect features and robust connectors facilitate efficient cable management and troubleshooting.
Environmentally Friendly Materials:
There’s a growing emphasis on developing servo motor cables using environmentally friendly materials and manufacturing processes. This aligns with broader sustainability initiatives in various industries.
Customization and Modular Solutions:
Cable manufacturers are increasingly offering customizable solutions to meet the specific needs of different applications. Modular cable designs allow users to tailor cables to their exact requirements.
It’s recommended to check with cable manufacturers and industry publications for the most recent advancements and innovations in servo motor cable technology, as the field is continuously evolving.